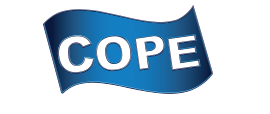
Finding Profitability and Sustainability in Plastics
Since the mid-1940’s, Cope Plastics has been known as a premier distributor and fabricator of plastic sheet, rod and tube in the Midwest. Today Cope strives to continue on its long-held mission of making the world a better place through sustainable partnerships and practices.
With the fabrication of plastic parts, Cope generates a high volume of scrap plastic, now deemed to have value worth harvesting. Today, Cope moves more than 2.5 million pounds of recyclable plastic chunks, generating more than $500,000 annual revenue.
As Cope’s business model expanded to address an ever-growing market, proficiency – and efficiency – at processing these materials with limited resources became more important. A key factor for meeting business objectives was the development of a financially sustainable program – one that could stand alone.
Andy Fergurson describes their key challenge this way: “Although our book of clients was growing, our resources needed to be held in check. Consequently capacity became and issue, and we only had so much space, manpower, and time to allocated to this process.”
When capacity became an issue, it showed – with disappointed customers and lost business. Shrinking margins due to increased resource costs also hit hard.
“We needed to zero in on our most profitable business, and which materials brought highest margins while requiring the least resources. In other words, what would allow us to maximize profit without increasing expense?”
Cope tried creating a solution that consisted of manual entry of the disparate data needed to make such decisions into spreadsheets on a shared drive. The result was cumbersome and unmanageable. Not to mention that only one user at a time could update the spreadsheet, and multiple users meant high chance for error.
Using Smart EOL from Eco-Catalyst, real time data and analytics accessible through an easy to use multi-user interface, gave Cope Plastics the decision support it needed to make the best decisions possible for its operations.
“Smart EOL allowed us to forecast better and make better choices at the agent level – instead of directing all decisions through management. Compiling the necessary data into one location helped us maximize the profitability from our limited resources.”
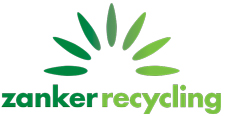
Zanker Recycling: From Landfill to Bay Area Recycling Power House
Zanker Recycling in San Jose, CA originally got its start as a landfill operation. From there it quickly developed into a major full service, resource management, composting/recycling facility and landfill for residents and commercial businesses in the area. From its inception, Zanker has challenged the industry standard and reset the bar for waste recycling. Zanker places high value on the materials that pass through its facilities – monetary, social and environmental – and considers condemning them to a landfill as a failure to maximize this value.
As San Jose continues to grow dramatically so had the Zanker operation. Today, separate areas of the facility handle the different waste materials and perform Demolition Debris Recycling, Asphalt Shingle Processing, Concrete Recycling and Wood Waste/Brush Recycling. The facility is also home to Zanker Landscape Materials, selling landscape and construction products they have recovered, and other landscape supplies as well.
In 1999, the Zanker Material Processing Facility, ZMPF, began recycling operations, with several processing areas, each capable of processing different types of waste streams. The Sheetrock Processing Area, Soils processing area and Mixed Construction Wastes Recycling today process over 900,000 tons of materials annually.
The Profitability Challenge
“The lack of reliable information is our worst enemy,” says Michael Gross, of Zanker Recycling. “We operate six different recycling operations on our property, each interacting with the next. Although we may understand the financial statement at the end of the month, it became critical for us to understand how each operation was providing – or not. This information had significant impact on our day-to-day decision-making regarding tipping fees. Without viable information for each recycling operation, we could not determine how to adjust our tipping fees, or even understand the real impacts of these fees.”
This challenge reduced Zanker’s profits, was a competitive disadvantage, and even reduced its recycling rates. An update to its scale system software helped with the reliability of its data, but still did not allow the opportunity to look at data over long periods of time, or to have a complete understanding of what materials were being recycled.
By implementing Smart EOL, Zanker can now track all data by operation and also take into consideration the impacts from each of its operations. The access to real-time data and analytics in Smart EOL allow “what if” analysis to determine future revenues and expenses, and expenses as well as projections of tonnages of recyclables. The result? The ability to plan for future changes in the commodities markets.
One benefit of using Smart EOL came as a surprise to Michael and his team at Zanker. “According to our financial records, one of our operations was continually under performing. Using the charting abilities of Smart EOL, our materials management determined that a large portion of revenues was not being adequately accounted for. It turned out, that recycling operation didn’t have performance problem at all!”
Operationally, Zanker has been able to leverage the visibility into expenses to make several smaller capital improvements in order to capture better data, enabling a streamlining of expenses and an increase in profitability. Additionally, because of improved data management, Zanker can confidently purchase its next recycling operation – an investment that will ultimately reduce expenses and increase profits. And according to Michael Gross, the end result of optimization provided through Smart EOL, Zanker’s overall recycling rate will increase by 5% – very significant when overall processing runs about 900,000 tons annually.
Currently Zanker has one user of Smart EOL and plans to expand to all of its facility managers, as well as to install Smart EOL at three of its other recycling operations in separate rollouts.